Experience Mastery of Inventory Control and Efficiency Unleashed
Register For Free Trial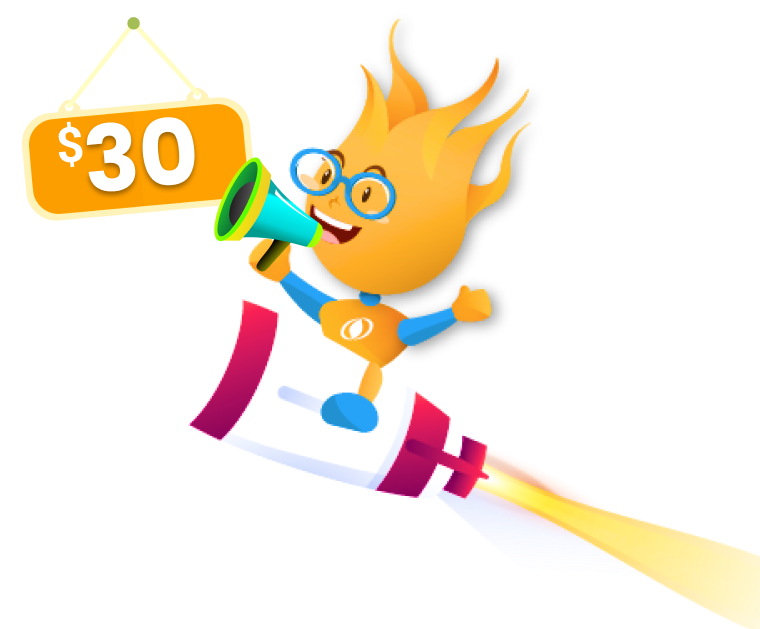
Opening Stock
Opening Stock represents the quantity of items or materials available in inventory at the beginning of a financial period or when the system is initially set up.
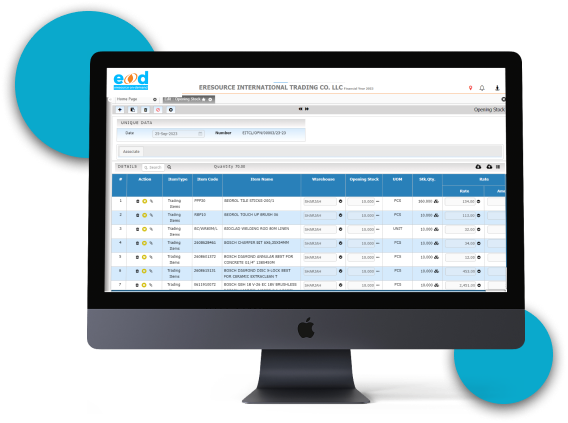
- Initialize opening stock quantities and values during system setup.
- Update opening stock values periodically to align with real-world inventory levels.
Stock Adjustment Increases
Stock Adjustment Increases are used to record and adjust inventory levels when items are added to inventory for reasons like purchases or transfers.
- Create adjustment entries to increase stock quantities.
- Specify reasons for adjustments, such as purchases or stock transfers.
Stock Adjustment Decreases
Stock Adjustment Decreases are used to record and adjust inventory levels when items are removed from inventory for reasons like damage or wastage.
- Create adjustment entries to decrease stock quantities.
- Specify reasons for adjustments, such as damaged items or wastage.
Material Requisition
Material Requisition is the process of requesting materials or items from the inventory for use in various operations or projects.
- Create material requisitions specifying the items, quantities, and purpose
- Route requisitions for approval before material issuance
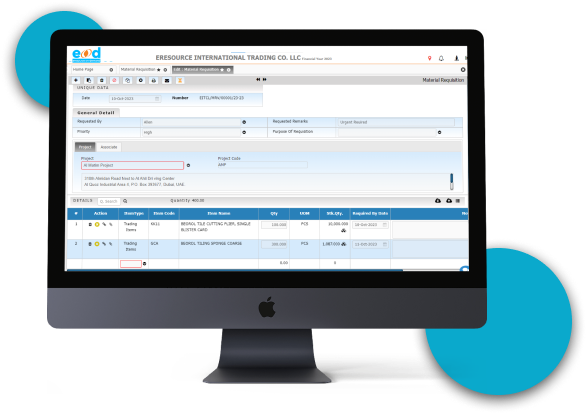
Material Receipt Note (MRN)
The Material Receipt Note module is used to record the receipt of materials or items into inventory from suppliers or other sources
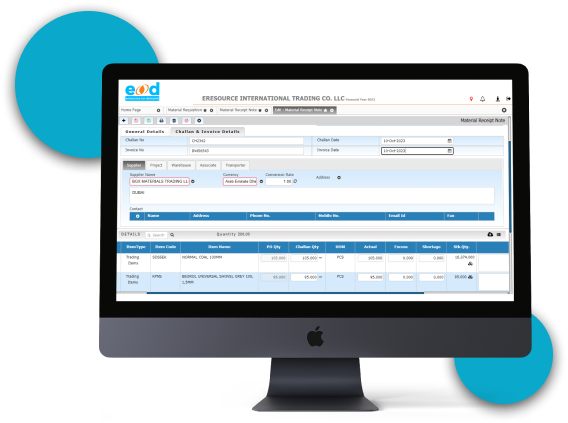
- Receive and inspect items as they arrive.
- Verify the quantity, quality, and condition of received goods.
- Update inventory records with received quantities.
Delivery Note
The Delivery Note module enables the creation of delivery notes that accompany shipments to customers or project sites
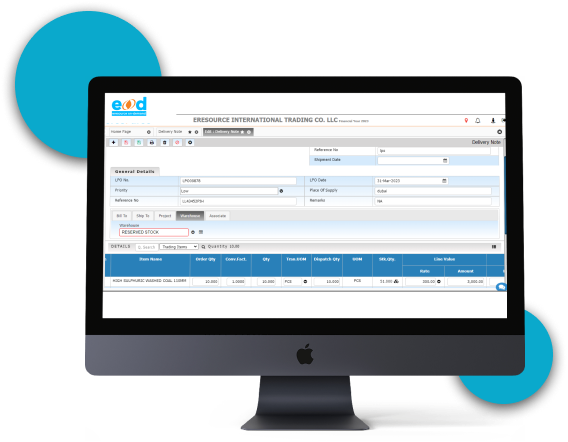
- Generate delivery notes specifying the items, quantities, and delivery details.
- Ensure accurate deliveries to customers or project locations.
Delivery Acknowledgment
Record acknowledgments of delivery from customers or project sites, confirming the receipt of items.
- Acknowledge deliveries to validate the receipt of items
- Update inventory records delivery con firmations.
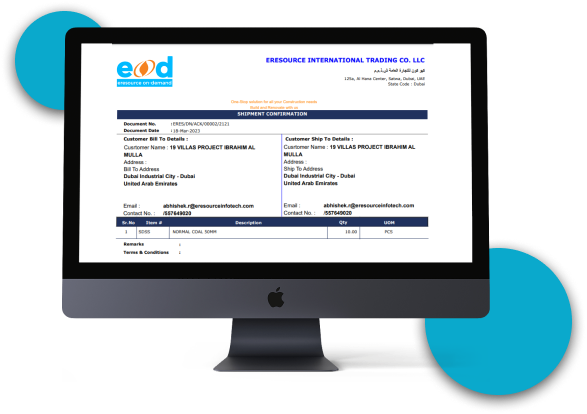
Purchase Return
Manage the return of items to suppliers due to defects or discrepancies in the items received.
- Record purchase returns and specify the reason, such as defective items or incorrect quantities
- Initiate the return process and track refunds or replacements.
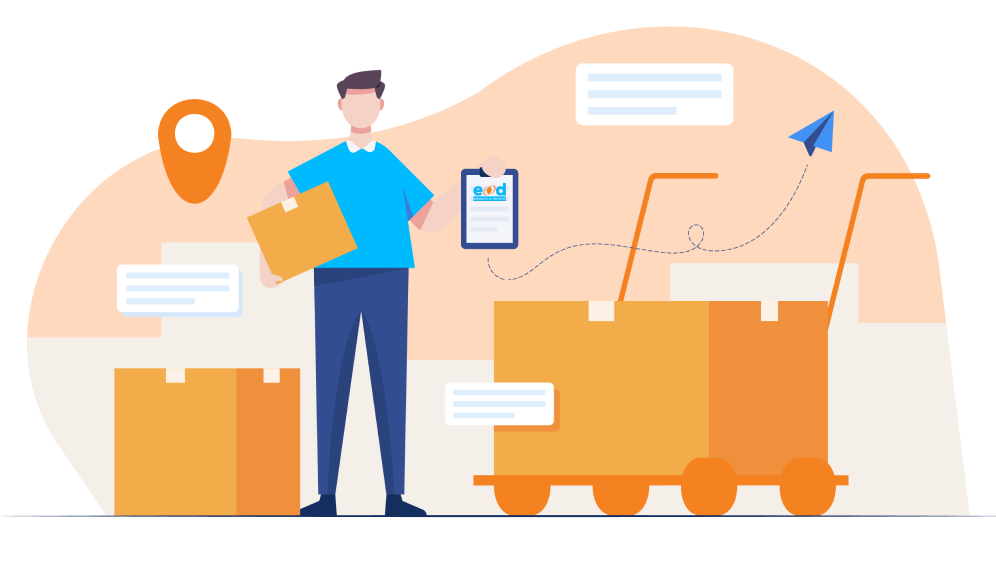
Sales Return
Handle customer returns and e changes when items are defective or not as expected.
- Record sales returns and specify the reason for the return
- Process returns, issue refunds or replacements, and update inventory records.
Material Issue
M aterial Issue involves the issuance of materials or items from inventory for various purposes, such as production or project needs.
- Create material issue records specifying the items, quantities, and purpose
- Deduct issued quantities from inventory.
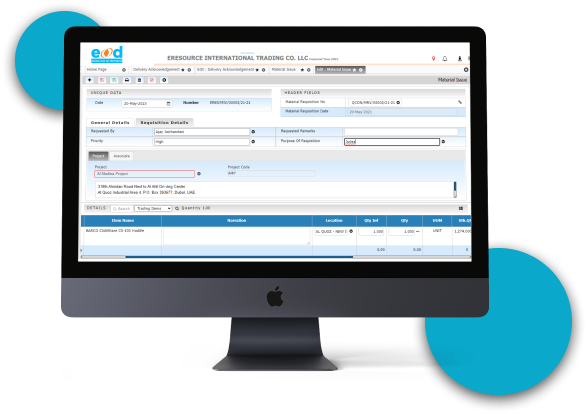
Stock Transfer
Facilitate the transfer of items between different warehouses, locations, or departments.
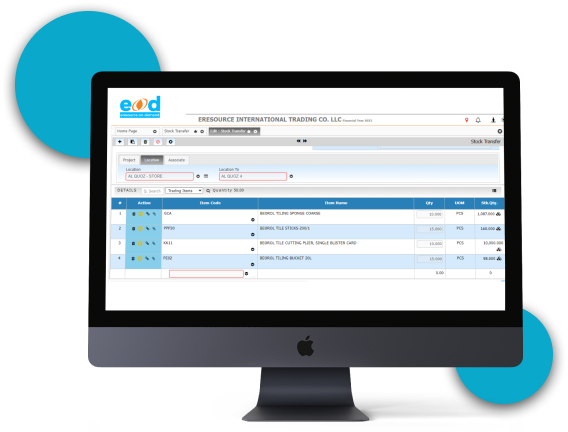
- Initiate stock transfers, specifying source and destination locations.
- Track the movement of items and update inventory records accordingly.